well, thanks for all the info !
i am slowly making progress (remember rule number 1, remember rule number 1...)
i followed your advice, and managed to work something out with the sleeve i had pulled out:
i sliced the top off, and made a slit with the dremel, so that i can use a flat screw driver to drive it on the thread. that's step number one.
next, i manufactured some sort of spacer, to press on the shoulder in the wood a little earlier. (if i got it right, that was the idea behind your suggestion of using washers.)
so far so good.
I drove the new bit in the neck, but the spacer was too long, i couldnt get a grip on the rod. so i pulled the lot out, and by magic, the rod came out too !
so i guess i have the whole lot out of the neck. but it doesnt look like i would have expected :
the rod is inside a plastic sleeve, and there is also a piece of square metal that runs alongside it, inside the sleeve. so the tross rod is effectively a 2 part thing.
the shearing i had seen on the first bit i took out was supposed to be attached to that square piece.
now i dont really understand how those bits work together ! i would have expected an anchor at the bottom of the neck, for the rod, but there isnt such a thing after all !
here is a poor picture of what this lot looks like:
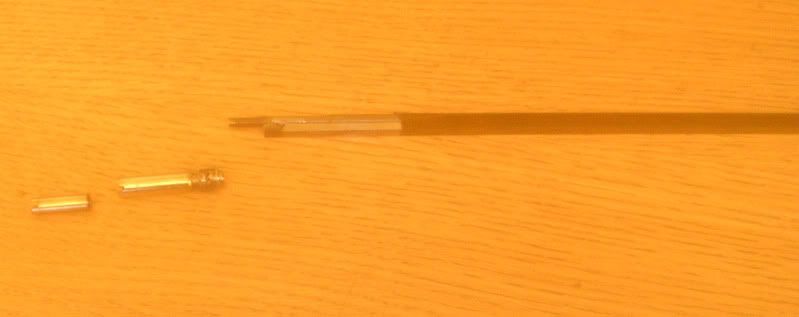
from left to right: the long "nut", originally with allen socket, now with slit for flat driver.
the sleeve, with a spacer on the end, to press earlier on the shoudler, and the truss rod assembly.
from the shearing, it looks like the sleave should be attached to the square piece.
i am off to try and find out out this works.